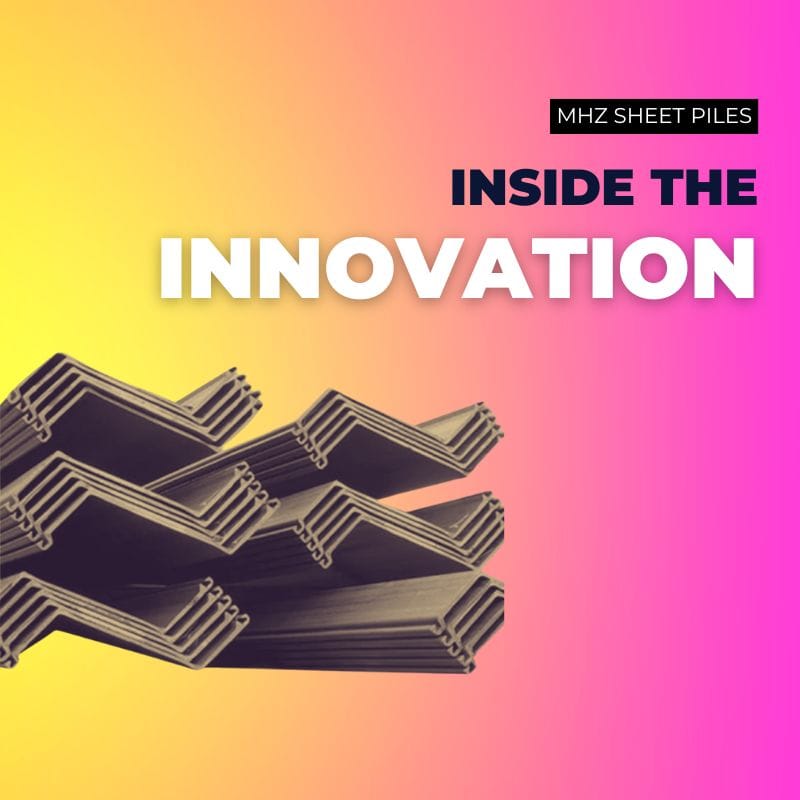
In the world of construction and civil engineering, sheet piles play a critical role in creating stable foundations, retaining walls, and waterfront structures. Among the industry’s leading products, MHZ sheet piles have earned a reputation for exceptional quality and performance. But have you ever wondered how MHZ sheet piles are made? This article takes you behind the scenes to explore the sophisticated manufacturing process that transforms raw materials into these essential construction components.
Raw Materials: The Foundation of Quality
The journey of how MHZ sheet piles are made begins with the careful selection of raw materials. Unlike conventional steel products, MHZ sheet piles utilize a specialized blend of:
- High-grade iron ore with specific mineral compositions
- Premium coal for coking processes
- Precisely measured alloying elements including manganese, silicon, and chromium
- Recycled steel that meets strict quality standards
This meticulous selection process ensures that every MHZ sheet pile starts with the optimal chemical composition for strength, durability, and corrosion resistance. According to the World Steel Association, the quality of raw materials directly impacts the final performance of steel products.
The Steelmaking Process
The first major step in how MHZ sheet piles are made involves transforming raw materials into high-quality steel. This process includes:
1. Smelting and Refining
The carefully selected raw materials enter blast furnaces where temperatures reach approximately 1,600°C (2,900°F). Here, the iron ore is reduced to molten iron while impurities are removed. This molten iron is then transferred to a basic oxygen furnace where:
- Oxygen is blown through the molten metal to reduce carbon content
- Precise amounts of alloying elements are added to achieve the desired steel grade
- Advanced computer systems monitor and control the chemical composition in real-time
2. Continuous Casting
Once the steel composition is perfected, the molten metal flows into a continuous casting machine. This critical step in how MHZ sheet piles are made transforms liquid steel into semi-finished slabs:
- The molten steel passes through water-cooled copper molds
- The outer shell solidifies while the inner core remains molten
- Support rollers guide the solidifying steel through the machine
- Cutting torches slice the continuous strand into predetermined lengths
The resulting steel slabs typically measure 200-250mm thick, 1,200-1,600mm wide, and 5-10m long, providing the raw material for the next stage of production.
Hot Rolling: Shaping the Profile
The semi-finished steel slabs must undergo significant transformation to become the distinctive Z or U profiles characteristic of MHZ sheet piles. This hot rolling process is perhaps the most fascinating part of how MHZ sheet piles are made:
1. Reheating
Before rolling can begin, the steel slabs are reheated in specialized furnaces:
- Temperatures reach approximately 1,200°C (2,200°F)
- Computer-controlled heating ensures uniform temperature throughout the slab
- This heat makes the steel malleable enough for the precise shaping required
2. Roughing Mill
The heated slabs first pass through the roughing mill, where:
- Heavy-duty rollers apply tremendous pressure to reduce thickness
- The slab’s width increases as its thickness decreases
- Multiple passes gradually transform the slab into a thinner plate
3. Profile Rolling
The most technically advanced stage of how MHZ sheet piles are made is the profile rolling process:
- Specialized rollers with precisely engineered contours shape the steel
- Multiple rolling stands progressively form the distinctive Z or U profile
- Computer-controlled positioning ensures exact dimensions and tolerances
- Advanced cooling systems maintain optimal metal temperature throughout the process
As noted by the American Institute of Steel Construction, this precision rolling is what gives modern sheet piles their superior strength-to-weight ratio compared to earlier designs.
Forming the Interlocks
One of the most critical aspects of how MHZ sheet piles are made is the formation of the interlocking system. These precision-engineered connections allow multiple sheet piles to join securely, creating continuous walls:
1. Interlock Milling
Specialized milling equipment creates the male and female interlock components:
- Computer-guided cutting tools shape the intricate geometries
- Tolerances are maintained within fractions of a millimeter
- Surface finish is carefully controlled to ensure smooth connections
2. Testing and Verification
Each interlock undergoes rigorous testing:
- Dimensional inspection with laser measurement systems
- Test assemblies to verify proper connection
- Tension testing to confirm structural integrity
- Water-tightness verification for hydraulic applications
Surface Treatment and Finishing
The final stage in how MHZ sheet piles are made involves preparing the surface for optimal performance in various environments:
1. Surface Preparation
Before any coatings can be applied:
- Automated shot blasting removes mill scale and creates an optimal surface profile
- Cleaning systems remove any residual contaminants
- Quality inspection verifies surface preparation meets standards
2. Protective Coatings
Depending on the intended application, MHZ sheet piles may receive specialized coatings:
- Corrosion-resistant primers for extended service life
- Bituminous coatings for groundwater protection
- Epoxy systems for marine environments
- Custom coatings for highly aggressive conditions
Quality Control Throughout Production
Rigorous quality control is integrated into every aspect of how MHZ sheet piles are made:
- Raw material testing and certification
- In-process monitoring with advanced sensors
- Dimensional verification using laser measuring systems
- Mechanical property testing including tensile, yield, and impact tests
- Ultrasonic inspection for internal defects
- Third-party certification for critical applications
Environmental Considerations
Modern manufacturing of MHZ sheet piles incorporates sustainable practices:
- Energy recovery systems that capture and reuse heat
- Water recycling throughout the production process
- Dust collection and air filtration systems
- Use of recycled steel as raw material input
- Waste minimization and byproduct utilization
Conclusion
The process of how MHZ sheet piles are made represents a remarkable fusion of traditional steelmaking and cutting-edge manufacturing technology. From raw material selection to final coating application, each step contributes to creating construction components that offer superior performance in challenging environments.
Understanding this manufacturing journey helps engineers and contractors appreciate why MHZ sheet piles deliver exceptional structural integrity, durability, and ease of installation across diverse applications. As construction demands continue to evolve, the innovative production methods behind these essential components will likewise continue to advance.